Destylacja rozpuszczalników to proces, który polega na oddzieleniu składników mieszaniny na podstawie różnic w ich temperaturach wrzenia. W praktyce oznacza to, że podczas podgrzewania cieczy, składniki o niższej temperaturze wrzenia parują jako pierwsze, a następnie są skraplane i zbierane w osobnym naczyniu. Kluczowym elementem tego procesu jest kolumna destylacyjna, która umożliwia wielokrotne skraplanie i parowanie, co zwiększa czystość uzyskanego produktu. W przypadku destylacji rozpuszczalników często stosuje się również różne techniki, takie jak destylacja frakcyjna, która pozwala na oddzielenie wielu składników z mieszaniny. Ważnym aspektem jest również dobór odpowiednich materiałów, które nie będą reagować z destylowanymi substancjami oraz zapewnienie odpowiednich warunków pracy, takich jak ciśnienie i temperatura.
Jakie są zastosowania destylacji rozpuszczalników w przemyśle
Destylacja rozpuszczalników znajduje szerokie zastosowanie w różnych gałęziach przemysłu, od chemicznego po spożywczy. W przemyśle chemicznym proces ten jest kluczowy dla oczyszczania substancji chemicznych oraz separacji składników w reakcjach chemicznych. Dzięki destylacji można uzyskać wysokiej czystości produkty, które są niezbędne do dalszych procesów produkcyjnych. W przemyśle farmaceutycznym destylacja jest wykorzystywana do produkcji leków oraz ich składników aktywnych. Oczyszczanie substancji poprzez destylację pozwala na usunięcie zanieczyszczeń oraz niepożądanych składników, co jest niezwykle istotne dla jakości finalnych produktów. W branży spożywczej destylacja jest stosowana do produkcji alkoholi oraz aromatów. Proces ten pozwala na uzyskanie czystych esencji smakowych i zapachowych, które są wykorzystywane w produkcji żywności i napojów.
Jakie są najważniejsze rodzaje destylacji rozpuszczalników
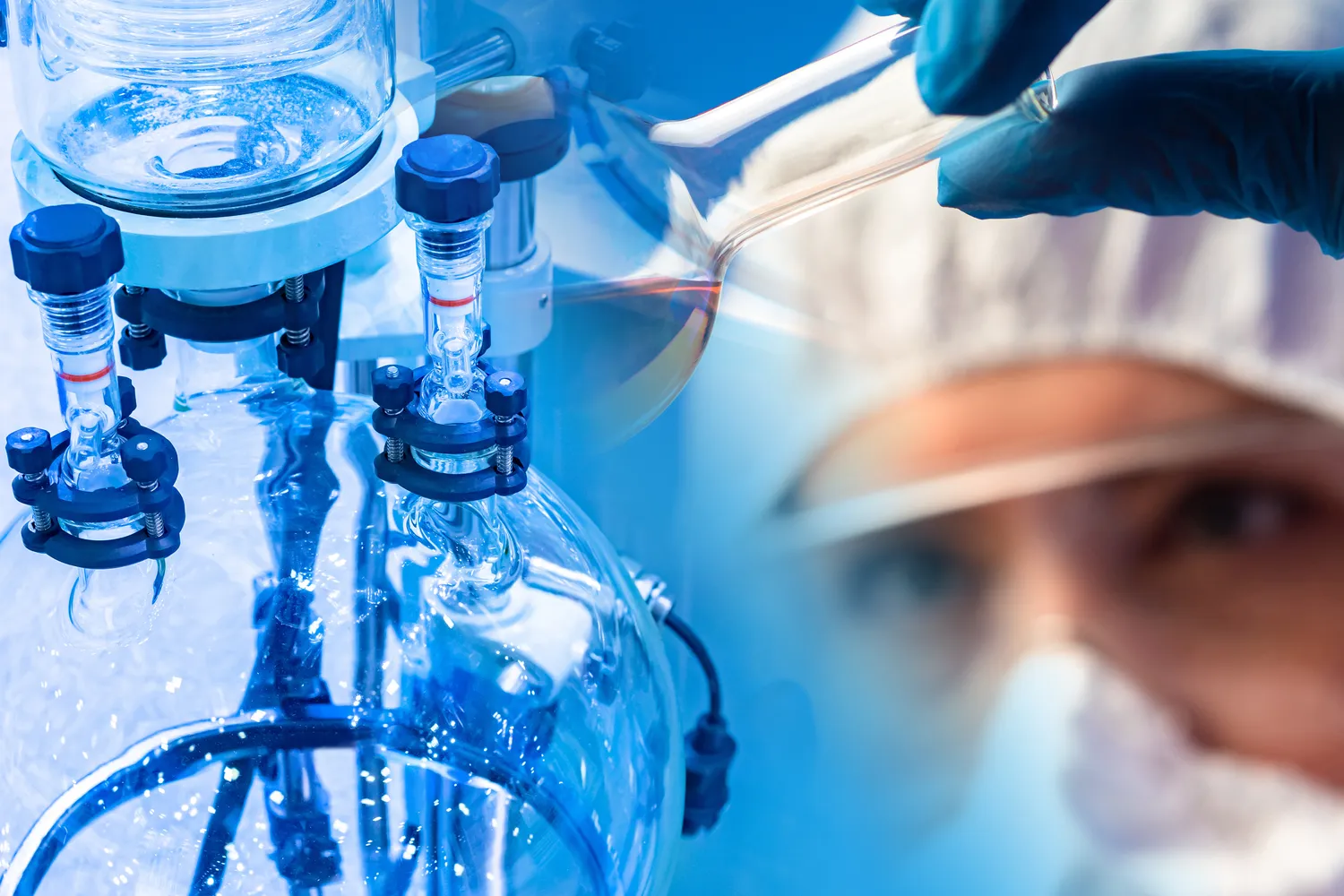
W kontekście destylacji rozpuszczalników wyróżnia się kilka kluczowych metod, które różnią się między sobą zastosowaniem oraz efektywnością. Najpopularniejszą formą jest destylacja prosta, która polega na jednorazowym podgrzewaniu cieczy i zbieraniu pary w formie skroplonej. Jest to metoda stosunkowo łatwa i tania, jednak ma swoje ograniczenia w przypadku mieszanin o zbliżonych temperaturach wrzenia. Dlatego w takich przypadkach lepszym rozwiązaniem jest destylacja frakcyjna, która wykorzystuje kolumny destylacyjne do wielokrotnego skraplania i parowania składników. Dzięki temu możliwe jest uzyskanie wyższej czystości produktów końcowych. Innym rodzajem jest destylacja azeotropowa, która pozwala na oddzielanie składników tworzących azeotrop – mieszanin o stałym składzie w stanie ciekłym i gazowym. Warto również wspomnieć o destylacji pod ciśnieniem atmosferycznym oraz pod próżnią, które mają zastosowanie w przypadku substancji wrażliwych na wysoką temperaturę lub łatwo parujących.
Jakie są zalety i wady różnych metod destylacji
Każda metoda destylacji rozpuszczalników ma swoje zalety i wady, które warto rozważyć przed podjęciem decyzji o wyborze konkretnej techniki. Destylacja prosta jest jedną z najłatwiejszych metod do przeprowadzenia i wymaga minimalnych nakładów finansowych oraz sprzętowych. Jej główną wadą jest ograniczona skuteczność w separowaniu składników o podobnych temperaturach wrzenia. Z kolei destylacja frakcyjna oferuje znacznie wyższą efektywność separacji dzięki zastosowaniu kolumny destylacyjnej, jednak wiąże się z większymi kosztami operacyjnymi oraz bardziej skomplikowanym procesem technologicznym. Destylacja azeotropowa może być niezwykle skuteczna w przypadku trudnych mieszanin, ale wymaga dodatkowych reagentów lub zmiany warunków pracy, co może zwiększać koszty procesu. Warto również zwrócić uwagę na wpływ różnych metod na środowisko – niektóre techniki mogą generować większe ilości odpadów lub emisji szkodliwych substancji.
Jakie są kluczowe czynniki wpływające na efektywność destylacji rozpuszczalników
Efektywność destylacji rozpuszczalników zależy od wielu czynników, które mogą znacząco wpłynąć na jakość i wydajność procesu. Jednym z najważniejszych aspektów jest temperatura wrzenia składników mieszaniny. Różnice w temperaturach wrzenia są kluczowe dla skutecznego oddzielania substancji, dlatego im większa różnica, tym łatwiejsze jest przeprowadzenie destylacji. Kolejnym istotnym czynnikiem jest ciśnienie atmosferyczne, które może być regulowane w celu obniżenia temperatury wrzenia substancji, co jest szczególnie przydatne w przypadku składników wrażliwych na wysoką temperaturę. Dodatkowo, konstrukcja kolumny destylacyjnej oraz zastosowane materiały mają ogromny wpływ na efektywność procesu. Wysokiej jakości materiały oraz odpowiednia geometria kolumny mogą zwiększyć powierzchnię kontaktu między parą a cieczą, co sprzyja lepszemu skraplaniu i parowaniu. Również prędkość przepływu pary oraz cieczy w kolumnie ma znaczenie – zbyt szybki przepływ może prowadzić do nieefektywnego oddzielania składników.
Jakie są najczęstsze problemy podczas destylacji rozpuszczalników
Podczas przeprowadzania destylacji rozpuszczalników można napotkać szereg problemów, które mogą wpłynąć na jakość i wydajność procesu. Jednym z najczęstszych problemów jest tworzenie się azeotropów, które mogą uniemożliwić skuteczne oddzielenie składników. Azeotropy to mieszaniny o stałym składzie, które nie zmieniają swojego stosunku nawet podczas destylacji. W takich przypadkach konieczne może być zastosowanie specjalnych technik, takich jak destylacja azeotropowa lub dodanie substancji pomocniczych. Innym problemem mogą być zanieczyszczenia w surowcach, które mogą prowadzić do obniżenia jakości końcowego produktu. Dlatego ważne jest, aby przed przystąpieniem do destylacji dokładnie oczyścić surowce oraz monitorować ich jakość. Dodatkowo, niewłaściwe ustawienia parametrów pracy, takich jak temperatura czy ciśnienie, mogą prowadzić do nieefektywnego oddzielania składników lub nawet uszkodzenia sprzętu.
Jakie są nowoczesne technologie wykorzystywane w destylacji rozpuszczalników
W ostatnich latach rozwój technologii wpłynął na sposób przeprowadzania destylacji rozpuszczalników, co pozwala na uzyskanie lepszej efektywności oraz jakości produktów końcowych. Nowoczesne systemy destylacyjne często wykorzystują zaawansowane technologie automatyzacji, które umożliwiają precyzyjne kontrolowanie parametrów procesu, takich jak temperatura czy ciśnienie. Dzięki temu możliwe jest osiągnięcie optymalnych warunków pracy oraz minimalizacja ryzyka wystąpienia błędów ludzkich. Ponadto, nowoczesne kolumny destylacyjne są projektowane z myślą o maksymalizacji powierzchni kontaktu między parą a cieczą, co zwiększa efektywność separacji składników. Wykorzystanie nanotechnologii oraz materiałów kompozytowych pozwala na budowę bardziej wydajnych i trwałych urządzeń. Warto również wspomnieć o zastosowaniu technologii membranowych, które stanowią alternatywę dla tradycyjnej destylacji i mogą być stosowane do separacji rozpuszczalników w sposób bardziej energooszczędny.
Jakie są różnice między destylacją a innymi metodami separacji
Destylacja to jedna z wielu metod separacji substancji chemicznych, jednak różni się od innych technik pod względem zasad działania oraz zastosowania. Na przykład ekstrakcja to proces polegający na wydobywaniu składnika z mieszaniny przy użyciu rozpuszczalnika; różni się on od destylacji tym, że nie opiera się na różnicach w temperaturze wrzenia, lecz na rozpuszczalności substancji w danym rozpuszczalniku. Inną popularną metodą separacyjną jest filtracja, która polega na oddzieleniu ciał stałych od cieczy lub gazu za pomocą porowatego materiału; filtracja jest skuteczna w przypadku mieszanin zawierających nierozpuszczalne cząstki, ale nie nadaje się do separacji cieczy o podobnych właściwościach fizykochemicznych. Chromatografia to kolejna technika separacyjna, która wykorzystuje różnice w powinowactwie składników do fazy stacjonarnej i ruchomej; jest to metoda bardziej skomplikowana i czasochłonna niż destylacja, ale pozwala na uzyskanie bardzo czystych produktów.
Jakie są przyszłe kierunki rozwoju technologii destylacji rozpuszczalników
Przyszłość technologii destylacji rozpuszczalników zapowiada się obiecująco dzięki ciągłemu postępowi naukowemu oraz technologicznemu. W miarę rosnącej świadomości ekologicznej i potrzeby zrównoważonego rozwoju przemysł chemiczny zaczyna poszukiwać bardziej energooszczędnych i ekologicznych metod produkcji. W tym kontekście rozwijane są nowe technologie oparte na wykorzystaniu energii odnawialnej oraz procesów katalitycznych, które mogą znacznie zmniejszyć zużycie energii podczas destylacji. Ponadto badania nad nowymi materiałami do budowy kolumn destylacyjnych oraz membran separacyjnych mogą przyczynić się do zwiększenia efektywności procesów separacyjnych. Istotnym kierunkiem rozwoju jest także automatyzacja procesów przemysłowych – inteligentne systemy zarządzania procesami pozwolą na lepsze monitorowanie warunków pracy oraz optymalizację parametrów procesu w czasie rzeczywistym. Warto również zauważyć rosnącą rolę technologii cyfrowych i sztucznej inteligencji w analizie danych procesowych oraz prognozowaniu wyników produkcji.
Jakie są kluczowe aspekty bezpieczeństwa w destylacji rozpuszczalników
Bezpieczeństwo podczas destylacji rozpuszczalników jest niezwykle istotne, ponieważ proces ten często wiąże się z używaniem substancji chemicznych, które mogą być łatwopalne lub toksyczne. Kluczowym aspektem jest zapewnienie odpowiedniej wentylacji w pomieszczeniach, gdzie odbywa się destylacja, aby zminimalizować ryzyko inhalacji szkodliwych oparów. Niezbędne jest również stosowanie odpowiednich środków ochrony osobistej, takich jak rękawice, gogle oraz odzież ochronna, aby zabezpieczyć pracowników przed kontaktem z niebezpiecznymi substancjami. Ważnym elementem jest także regularne przeglądanie i konserwacja sprzętu destylacyjnego, aby uniknąć awarii i wycieków. Wprowadzenie procedur awaryjnych oraz szkoleń dla pracowników dotyczących postępowania w przypadku sytuacji kryzysowych może znacząco zwiększyć bezpieczeństwo procesu. Dodatkowo, monitorowanie parametrów pracy, takich jak temperatura i ciśnienie, pozwala na wczesne wykrywanie nieprawidłowości i zapobieganie potencjalnym zagrożeniom.