Destylarka do rozpuszczalników to urządzenie, które wykorzystuje proces destylacji do oddzielania różnych substancji chemicznych na podstawie ich temperatury wrzenia. Działa to na zasadzie podgrzewania mieszaniny, co powoduje odparowanie substancji o niższej temperaturze wrzenia, a następnie skraplania jej w osobnym zbiorniku. Taki proces jest niezwykle przydatny w laboratoriach chemicznych oraz w przemyśle, gdzie często zachodzi potrzeba oczyszczania rozpuszczalników lub odzyskiwania cennych substancji. W praktyce destylarki mogą być wykorzystywane do produkcji czystych rozpuszczalników organicznych, takich jak etanol czy aceton, które są niezbędne w wielu procesach przemysłowych i badawczych. Oprócz tego, destylacja pozwala na usunięcie zanieczyszczeń z rozpuszczalników, co jest kluczowe dla zapewnienia wysokiej jakości produktów końcowych. Warto również dodać, że nowoczesne destylarki są często wyposażone w systemy automatyzacji, co zwiększa ich efektywność i ułatwia obsługę.
Jakie są rodzaje destylarek do rozpuszczalników i ich różnice
Na rynku dostępnych jest wiele rodzajów destylarek do rozpuszczalników, które różnią się między sobą konstrukcją oraz przeznaczeniem. Najpopularniejsze z nich to destylarki prostokątne oraz okrągłe. Destylarki prostokątne charakteryzują się większą powierzchnią parowania, co może przyspieszyć proces destylacji. Z kolei destylarki okrągłe często są stosowane w laboratoriach ze względu na swoją kompaktową budowę oraz łatwość w obsłudze. Innym istotnym podziałem jest klasyfikacja według sposobu chłodzenia pary. Możemy wyróżnić destylarki z chłodzeniem wodnym oraz powietrznym. Chłodzenie wodne jest bardziej efektywne i powszechnie stosowane w przemyśle, natomiast chłodzenie powietrzne może być używane w mniejszych instalacjach laboratoryjnych. Warto również zwrócić uwagę na destylarki próżniowe, które umożliwiają przeprowadzanie procesów w obniżonym ciśnieniu, co pozwala na destylację substancji o wysokiej temperaturze wrzenia bez ryzyka ich degradacji.
Jakie materiały są wykorzystywane do produkcji destylarek
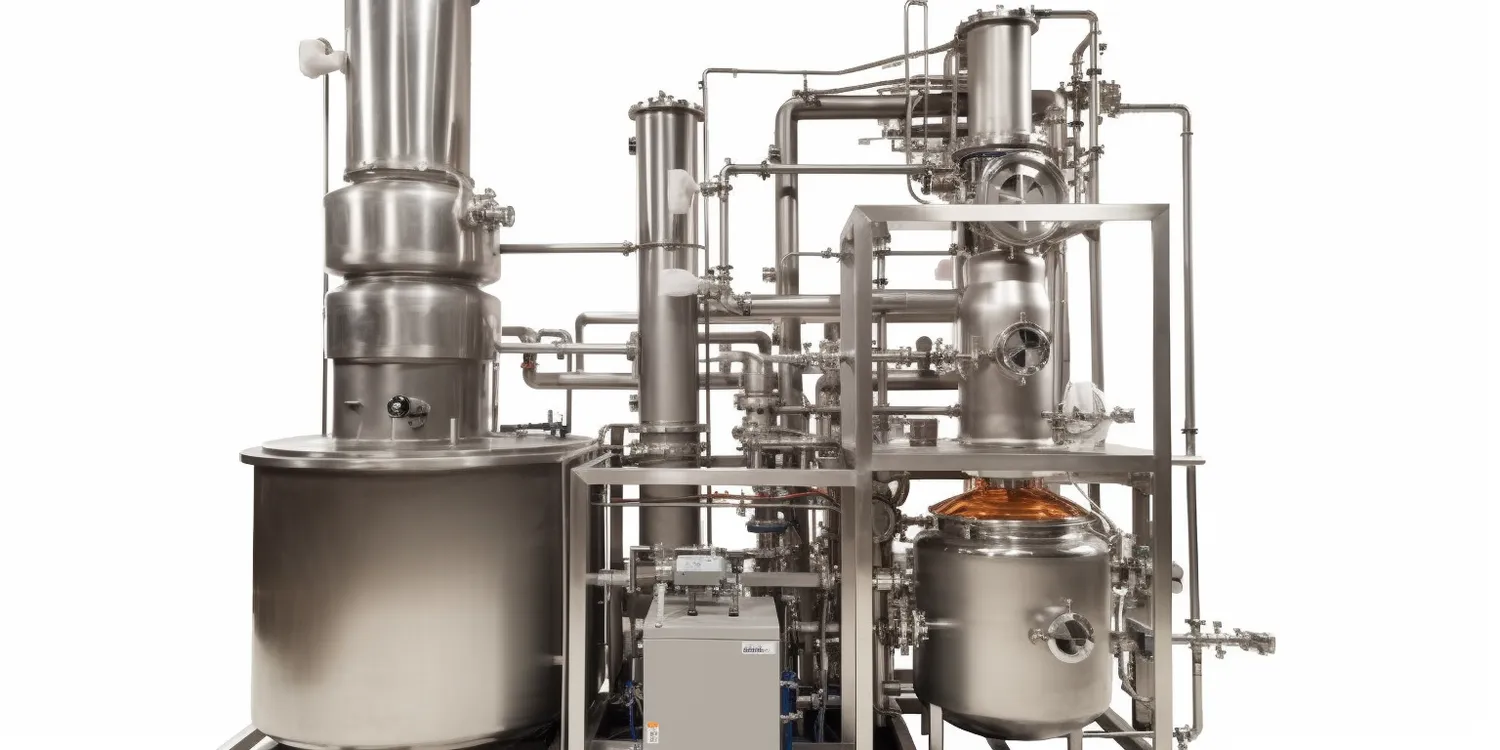
Produkcja destylarek do rozpuszczalników wymaga zastosowania odpowiednich materiałów, które zapewnią trwałość oraz odporność na działanie chemikaliów. Najczęściej wykorzystywanym materiałem jest stal nierdzewna, która charakteryzuje się wysoką odpornością na korozję oraz łatwością w utrzymaniu czystości. Stal nierdzewna jest idealnym wyborem dla przemysłowych instalacji, gdzie konieczne jest zachowanie najwyższych standardów higieny. Innym popularnym materiałem jest szkło borokrzemowe, które znajduje zastosowanie głównie w laboratoriach. Szkło borokrzemowe jest odporne na wysokie temperatury oraz działanie wielu chemikaliów, co czyni je doskonałym materiałem do budowy elementów destylacyjnych. W przypadku bardziej zaawansowanych technologii można spotkać również destylarki wykonane z materiałów kompozytowych lub specjalnych stopów metali, które oferują jeszcze lepsze właściwości mechaniczne i chemiczne. Ważnym aspektem przy wyborze materiału jest także jego wpływ na jakość finalnego produktu – niektóre materiały mogą reagować z substancjami chemicznymi, co prowadzi do kontaminacji końcowego produktu.
Jakie są kluczowe czynniki wpływające na wydajność destylarki
Wydajność destylarki do rozpuszczalników zależy od wielu czynników, które mogą wpływać na efektywność całego procesu. Przede wszystkim istotna jest temperatura podgrzewania – im wyższa temperatura, tym szybciej zachodzi proces odparowania substancji o niższej temperaturze wrzenia. Jednak należy pamiętać o tym, aby nie przekraczać optymalnej temperatury dla danej substancji, ponieważ może to prowadzić do jej degradacji lub niepożądanych reakcji chemicznych. Kolejnym ważnym czynnikiem jest ciśnienie atmosferyczne – w przypadku destylacji próżniowej obniżenie ciśnienia pozwala na przeprowadzenie procesu w niższej temperaturze, co zwiększa wydajność i jakość uzyskanego produktu. Również czas trwania procesu ma znaczenie – zbyt krótki czas może skutkować niedostatecznym oczyszczeniem substancji, natomiast zbyt długi czas może prowadzić do strat cennych składników. Nie bez znaczenia są także parametry konstrukcyjne samej destylarki – odpowiednia geometria kolumny destylacyjnej czy jakość zastosowanych materiałów mają kluczowy wpływ na efektywność separacji substancji.
Jakie są najczęstsze problemy z destylarkami do rozpuszczalników
Podczas użytkowania destylarek do rozpuszczalników mogą wystąpić różnorodne problemy, które mogą wpływać na ich wydajność oraz jakość uzyskiwanych produktów. Jednym z najczęściej spotykanych problemów jest zatykanie się kolumny destylacyjnej, co może być spowodowane osadzaniem się zanieczyszczeń lub nieodpowiednim doborem materiałów. Zatykanie kolumny prowadzi do obniżenia efektywności procesu oraz może powodować straty cennych substancji. Innym istotnym problemem jest niewłaściwe ustawienie temperatury podgrzewania, co może skutkować niepełnym oddzieleniem substancji i wprowadzeniem do produktu końcowego niepożądanych zanieczyszczeń. Warto również zwrócić uwagę na system chłodzenia – niewystarczająca wydajność chłodzenia może prowadzić do nieefektywnego skraplania par, co obniża ogólną wydajność destylacji. Dodatkowo, w przypadku destylarek próżniowych, niewłaściwe utrzymanie ciśnienia może prowadzić do problemów z odparowaniem substancji. Regularne przeglądy techniczne oraz konserwacja urządzeń są kluczowe dla zapobiegania tym problemom i zapewnienia długotrwałej oraz efektywnej pracy destylarki.
Jakie są koszty zakupu i eksploatacji destylarki do rozpuszczalników
Koszty zakupu i eksploatacji destylarki do rozpuszczalników mogą się znacznie różnić w zależności od jej typu, wielkości oraz zastosowania. Na rynku dostępne są zarówno małe, laboratoryjne destylarki, które można nabyć za kilka tysięcy złotych, jak i duże instalacje przemysłowe, których cena może sięgać setek tysięcy złotych. Wybór odpowiedniego urządzenia powinien być uzależniony od specyfiki działalności oraz przewidywanej wydajności. Oprócz kosztu zakupu warto również uwzględnić wydatki związane z eksploatacją urządzenia. Należy pamiętać o kosztach energii potrzebnej do podgrzewania substancji oraz chłodzenia par. Dodatkowo, regularna konserwacja i serwisowanie destylarki wiążą się z dodatkowymi wydatkami, które mogą znacząco wpłynąć na całkowity koszt użytkowania. Warto także rozważyć koszty związane z zakupem materiałów eksploatacyjnych, takich jak uszczelki czy filtry, które mogą wymagać okresowej wymiany.
Jakie są zalety korzystania z nowoczesnych destylarek do rozpuszczalników
Nowoczesne destylarki do rozpuszczalników oferują szereg zalet, które czynią je atrakcyjnym rozwiązaniem zarówno dla laboratoriów, jak i przemysłu. Przede wszystkim charakteryzują się one wysoką efektywnością energetyczną, co pozwala na znaczną redukcję kosztów eksploatacji. Dzięki zastosowaniu zaawansowanych technologii automatyzacji proces destylacji staje się bardziej precyzyjny i mniej czasochłonny, co zwiększa ogólną wydajność produkcji. Nowoczesne urządzenia często wyposażone są w systemy monitorowania parametrów pracy, co umożliwia bieżącą kontrolę nad procesem oraz szybką reakcję na ewentualne problemy. Kolejną istotną zaletą jest możliwość dostosowania ustawień destylacji do specyficznych potrzeb użytkownika, co pozwala na uzyskanie produktów o wysokiej czystości i jakości. Wiele nowoczesnych modeli posiada również funkcje samodiagnostyki oraz alarmowania o awariach, co zwiększa bezpieczeństwo użytkowania. Ponadto nowoczesne destylarki często wykonane są z materiałów odpornych na działanie chemikaliów oraz korozję, co zapewnia ich długowieczność i niezawodność.
Jakie są alternatywy dla tradycyjnych destylarek do rozpuszczalników
W kontekście oczyszczania rozpuszczalników istnieje kilka alternatyw dla tradycyjnych destylarek, które mogą być stosowane w różnych zastosowaniach przemysłowych i laboratoryjnych. Jedną z popularnych metod jest ekstrakcja cieczy cieczą, która polega na wykorzystaniu różnicy rozpuszczalności substancji w dwóch niemieszających się cieczy. Ta metoda jest szczególnie przydatna w przypadku separacji składników o podobnych temperaturach wrzenia. Inną alternatywą jest chromatografia, która pozwala na separację składników mieszaniny na podstawie ich różnic w interakcji z fazą stacjonarną i ruchomą. Chromatografia jest szeroko stosowana w laboratoriach analitycznych do oczyszczania substancji chemicznych oraz analizy ich składu. Można również spotkać metody takie jak adsorpcja czy membranowe procesy separacyjne, które wykorzystują różnice w właściwościach fizykochemicznych substancji do ich oddzielania. Każda z tych metod ma swoje zalety i ograniczenia, dlatego wybór odpowiedniej technologii powinien być uzależniony od specyfiki danej aplikacji oraz wymagań dotyczących jakości końcowego produktu.
Jakie są przepisy prawne dotyczące użytkowania destylarek do rozpuszczalników
Użytkowanie destylarek do rozpuszczalników wiąże się z przestrzeganiem określonych przepisów prawnych oraz norm bezpieczeństwa, które mają na celu ochronę zdrowia ludzi oraz środowiska naturalnego. W wielu krajach istnieją regulacje dotyczące przechowywania i używania substancji chemicznych, które obejmują również procesy związane z destylacją. Użytkownicy muszą zapewnić odpowiednie warunki pracy dla urządzeń oraz przestrzegać zasad BHP podczas obsługi destylarek. Ważnym aspektem jest także odpowiednie oznakowanie substancji chemicznych oraz prowadzenie dokumentacji dotyczącej ich użycia i przechowywania. W Polsce przepisy te regulowane są przez ustawę o chemikaliach oraz inne akty prawne dotyczące ochrony środowiska i zdrowia publicznego. W przypadku przemysłowego użytkowania destylarek konieczne może być uzyskanie odpowiednich zezwoleń oraz regularne przeprowadzanie audytów zgodności z obowiązującymi normami prawnymi.
Jakie innowacje technologiczne wpływają na rozwój destylarek
Innowacje technologiczne mają ogromny wpływ na rozwój destylarek do rozpuszczalników, przyczyniając się do poprawy ich wydajności oraz bezpieczeństwa użytkowania. W ostatnich latach pojawiły się nowe materiały konstrukcyjne, takie jak kompozyty czy stopy metali o wysokiej odporności chemicznej, które zwiększają trwałość urządzeń i umożliwiają pracę w trudnych warunkach. Również rozwój technologii automatyzacji sprawił, że nowoczesne destylarki są coraz bardziej inteligentne – wyposażone w systemy monitorujące parametry pracy pozwalające na bieżącą kontrolę procesu oraz automatyczne dostosowywanie ustawień w celu optymalizacji wydajności. Innowacyjne rozwiązania obejmują także zastosowanie sztucznej inteligencji do analizy danych operacyjnych oraz prognozowania potencjalnych awarii przed ich wystąpieniem. Ponadto rozwój technologii chłodzenia przyczynia się do zwiększenia efektywności skraplania par oraz redukcji zużycia energii podczas procesu destylacji.