Łączenie dwóch kompresorów to zadanie, które może przynieść wiele korzyści, zwłaszcza w kontekście zwiększenia wydajności systemu pneumatycznego. W pierwszej kolejności warto zrozumieć, jakie są różne metody łączenia kompresorów oraz jakie są ich zalety i wady. Istnieją dwa główne podejścia do tego zagadnienia: równoległe i szeregowe połączenie kompresorów. Połączenie równoległe polega na tym, że oba urządzenia pracują jednocześnie, co pozwala na zwiększenie przepływu powietrza. Taki układ jest szczególnie korzystny w sytuacjach, gdy potrzebna jest duża ilość sprężonego powietrza w krótkim czasie. Z drugiej strony, połączenie szeregowe oznacza, że jeden kompresor działa jako wsparcie dla drugiego, co może być przydatne w przypadku, gdy jeden z nich nie jest wystarczająco mocny, aby zaspokoić zapotrzebowanie.
Jakie narzędzia i materiały są potrzebne do połączenia kompresorów?
Aby skutecznie połączyć dwa kompresory, konieczne jest przygotowanie odpowiednich narzędzi i materiałów. Przede wszystkim będziemy potrzebować zestawu kluczy oraz śrubokrętów, które umożliwią nam montaż i demontaż poszczególnych elementów. Ważne jest także posiadanie manometru do pomiaru ciśnienia, co pozwoli nam na monitorowanie pracy systemu po zakończeniu instalacji. Dodatkowo warto zaopatrzyć się w rury i złączki pneumatyczne, które będą niezbędne do stworzenia odpowiednich połączeń między kompresorami. W przypadku połączenia równoległego istotne będzie także zastosowanie zaworów zwrotnych, które zapobiegną cofaniu się powietrza. Nie można zapomnieć o filtrach powietrza oraz oleju, które zapewnią czystość medium roboczego i ochronią urządzenia przed uszkodzeniami.
Jakie są najczęstsze błędy podczas łączenia kompresorów?
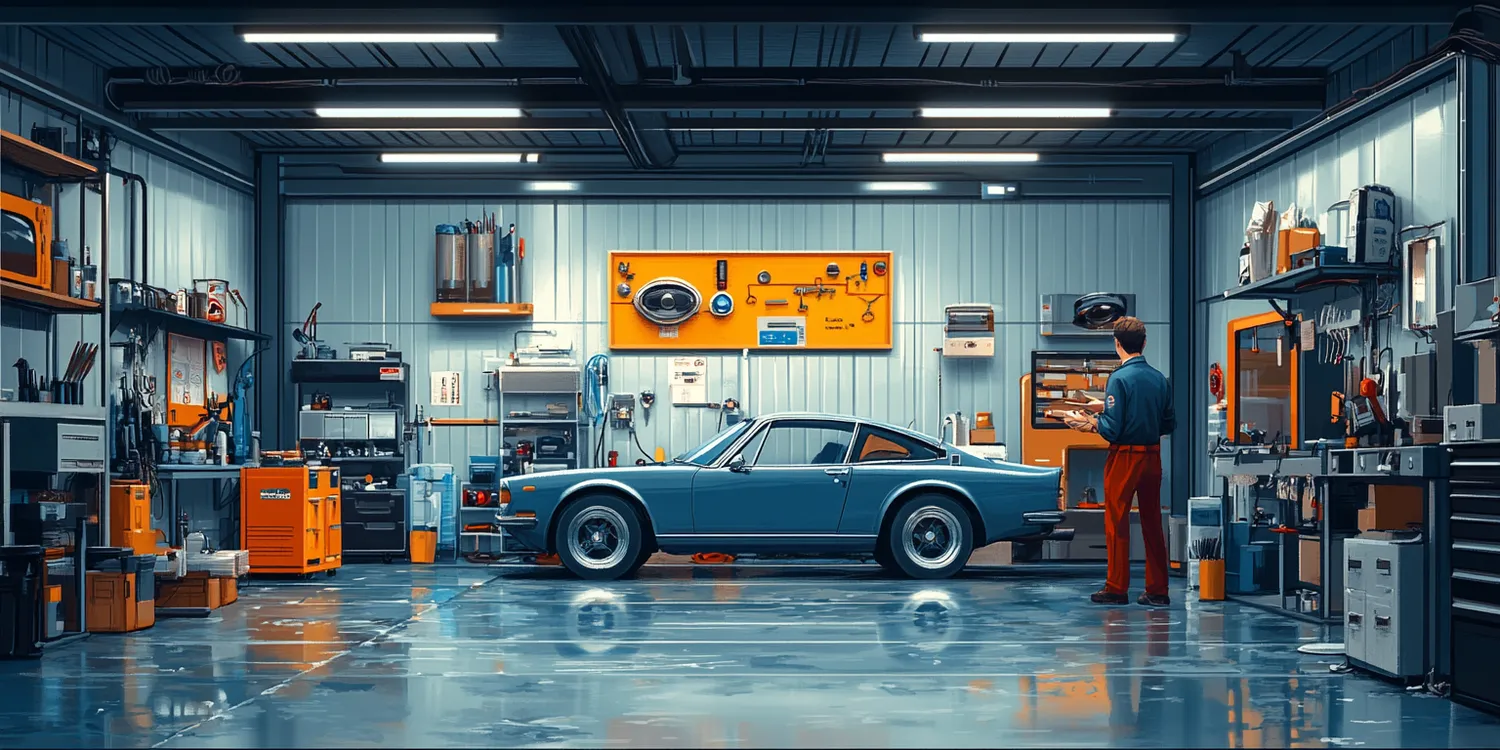
Podczas łączenia dwóch kompresorów istnieje wiele pułapek, w które można łatwo wpaść, dlatego warto być świadomym najczęstszych błędów. Jednym z najczęściej popełnianych błędów jest niewłaściwe dobranie parametrów technicznych obu urządzeń. Kompresory powinny mieć podobne wydajności oraz ciśnienia robocze, aby mogły współpracować ze sobą efektywnie. Innym powszechnym problemem jest niewłaściwe wykonanie połączeń pneumatycznych, co może prowadzić do wycieków powietrza i obniżenia efektywności całego systemu. Należy również pamiętać o odpowiednim zabezpieczeniu elektrycznym obu kompresorów; ich zasilanie powinno być dostosowane do wymagań obu urządzeń. Często zdarza się również ignorowanie potrzeby regularnej konserwacji i czyszczenia filtrów oraz innych elementów systemu, co może prowadzić do awarii sprzętu w dłuższym okresie użytkowania.
Jakie korzyści płyną z łączenia dwóch kompresorów?
Łączenie dwóch kompresorów niesie ze sobą szereg korzyści, które mogą znacząco wpłynąć na efektywność pracy systemu pneumatycznego. Przede wszystkim zwiększa to wydajność całego układu; dzięki równoległemu działaniu dwóch jednostek możliwe jest uzyskanie większego przepływu powietrza, co jest szczególnie istotne w przypadku intensywnych prac wymagających dużej ilości sprężonego powietrza. Dodatkowo połączenie kompresorów może przyczynić się do lepszego zarządzania energią; w sytuacji mniejszego zapotrzebowania jeden z kompresorów może zostać wyłączony, co pozwala na oszczędności energetyczne. Kolejną zaletą jest możliwość uzyskania większej niezawodności systemu; jeśli jeden z kompresorów ulegnie awarii, drugi nadal będzie mógł pracować, co minimalizuje ryzyko przestojów w produkcji czy innych procesach wymagających sprężonego powietrza.
Jakie są wymagania dotyczące instalacji dwóch kompresorów?
Instalacja dwóch kompresorów wymaga spełnienia określonych wymagań technicznych oraz przestrzennych, które zapewnią ich prawidłowe funkcjonowanie. Przede wszystkim, miejsce, w którym będą zainstalowane kompresory, musi być odpowiednio wentylowane, aby uniknąć przegrzewania się urządzeń. Warto również zwrócić uwagę na poziom hałasu generowanego przez kompresory; w przypadku pracy w zamkniętych pomieszczeniach może być konieczne zastosowanie dodatkowych środków wygłuszających. Kolejnym istotnym aspektem jest dostęp do źródła zasilania; kompresory powinny być podłączone do odpowiednich gniazd elektrycznych, które są w stanie dostarczyć wymagane napięcie i natężenie prądu. Należy także uwzględnić odpowiednie zabezpieczenia elektryczne, takie jak wyłączniki różnicowoprądowe, które chronią przed przeciążeniem i zwarciem.
Jakie są różnice między kompresorami tłokowymi a śrubowymi?
Wybór odpowiedniego typu kompresora jest kluczowy przy planowaniu połączenia dwóch jednostek. Kompresory tłokowe i śrubowe różnią się zasadniczo zarówno konstrukcją, jak i sposobem działania. Kompresory tłokowe działają na zasadzie zmiany objętości powietrza w cylindrze za pomocą ruchomego tłoka. Tego typu urządzenia charakteryzują się prostą budową oraz stosunkowo niskimi kosztami zakupu, co czyni je popularnym wyborem w małych warsztatach czy gospodarstwach domowych. Z kolei kompresory śrubowe wykorzystują mechanizm rotacyjny, w którym dwa wirniki obracają się względem siebie, sprężając powietrze. Dzięki temu rozwiązaniu kompresory śrubowe oferują znacznie wyższą wydajność oraz mniejsze zużycie energii, co czyni je idealnym wyborem dla dużych zakładów przemysłowych.
Jakie są zasady bezpieczeństwa podczas pracy z kompresorami?
Bezpieczeństwo pracy z kompresorami jest niezwykle istotne, szczególnie gdy mamy do czynienia z dwoma jednostkami działającymi jednocześnie. Przede wszystkim należy przestrzegać zasad BHP dotyczących obsługi sprzętu pneumatycznego. Osoby pracujące przy kompresorach powinny być odpowiednio przeszkolone i świadome potencjalnych zagrożeń związanych z ich użytkowaniem. Ważne jest również regularne przeprowadzanie konserwacji urządzeń; należy dbać o czystość filtrów powietrza oraz oleju, a także kontrolować stan techniczny wszystkich elementów układu pneumatycznego. Warto także stosować odpowiednie środki ochrony osobistej, takie jak rękawice czy okulary ochronne, aby zminimalizować ryzyko urazów. Dodatkowo zaleca się umieszczenie oznaczeń informujących o obecności sprzętu sprężonego powietrza oraz o zasadach postępowania w razie awarii lub wycieku powietrza.
Jakie są najczęstsze zastosowania dla połączonych kompresorów?
Połączone kompresory znajdują szerokie zastosowanie w różnych branżach przemysłowych oraz usługowych. Jednym z najpopularniejszych zastosowań jest produkcja sprężonego powietrza do napędu narzędzi pneumatycznych, takich jak wkrętarki czy młoty udarowe. Dzięki zwiększonej wydajności połączenia dwóch kompresorów możliwe jest efektywne zaspokojenie zapotrzebowania na sprężone powietrze w dużych zakładach produkcyjnych czy warsztatach rzemieślniczych. Kolejnym obszarem zastosowań jest przemysł motoryzacyjny; połączone kompresory mogą być wykorzystywane do lakierowania pojazdów czy obsługi systemów klimatyzacyjnych. W sektorze budowlanym sprężone powietrze jest niezbędne do obsługi różnorodnych maszyn budowlanych oraz narzędzi ręcznych. Połączenie dwóch kompresorów może również znaleźć zastosowanie w systemach chłodniczych oraz klimatyzacyjnych, gdzie wymagana jest duża ilość sprężonego powietrza do efektywnego działania całego układu.
Jakie są koszty związane z łączeniem dwóch kompresorów?
Koszty związane z łączeniem dwóch kompresorów mogą się znacznie różnić w zależności od wielu czynników, takich jak typ używanych urządzeń, materiały potrzebne do instalacji oraz robocizna związana z montażem. Na początek warto zwrócić uwagę na cenę samych kompresorów; jeśli decydujemy się na zakup nowego sprzętu, musimy uwzględnić ich koszt w budżecie projektu. Dodatkowo należy doliczyć wydatki związane z zakupem niezbędnych akcesoriów, takich jak rury, złączki czy zawory zwrotne. Koszt materiałów może się różnić w zależności od jakości i producenta; warto więc porównać oferty różnych dostawców przed podjęciem decyzji o zakupie. Nie można zapominać o kosztach robocizny; jeśli nie posiadamy odpowiednich umiejętności do samodzielnego montażu, konieczne będzie zatrudnienie specjalisty lub ekipy montażowej, co również wpłynie na całkowity koszt inwestycji.
Jakie są alternatywy dla łączenia dwóch kompresorów?
Choć łączenie dwóch kompresorów może przynieść wiele korzyści, istnieją również alternatywne rozwiązania, które mogą okazać się równie efektywne lub nawet bardziej korzystne w określonych sytuacjach. Jednym z takich rozwiązań jest zakup jednego większego kompresora o wyższej wydajności niż dwa mniejsze urządzenia razem wzięte. Taki wybór może okazać się bardziej opłacalny pod względem kosztów eksploatacji i konserwacji, ponieważ jedno urządzenie wymaga mniej uwagi niż dwa oddzielne kompresory. Inną alternatywą jest zastosowanie systemu magazynowania sprężonego powietrza; zbiornik ciśnieniowy pozwala na gromadzenie nadmiaru sprężonego powietrza i jego późniejsze wykorzystanie w momentach zwiększonego zapotrzebowania.
Jakie są najlepsze praktyki przy łączeniu dwóch kompresorów?
Aby zapewnić optymalne działanie połączonych kompresorów oraz minimalizować ryzyko awarii czy problemów eksploatacyjnych, warto stosować kilka najlepszych praktyk podczas ich instalacji i użytkowania. Przede wszystkim kluczowe jest dokładne zaplanowanie całego procesu łączenia; przed przystąpieniem do montażu należy sporządzić szczegółowy schemat instalacji oraz określić wszystkie niezbędne materiały i narzędzia. Ważne jest także regularne przeprowadzanie konserwacji obu urządzeń; należy dbać o czystość filtrów powietrza oraz oleju i kontrolować stan techniczny wszystkich elementów układu pneumatycznego.